General Caution (Electronic device products)
Caution
-
The products and the product specifications described in this document are subject to change or discontinuation of production without notice for reasons such as improvement. Therefore, before deciding to use the products, please refer to our sales representatives for the latest information thereon.
-
The materials in this document may not be copied or otherwise reproduced in whole or in part without the prior written consent of us.
-
This product and any technical information relating thereto are subject to complementary export controls (so-called KNOW controls) under the Foreign Exchange and Foreign Trade Law, and related politics ministerial ordinance of the law. (Note that the complementary export controls are inapplicable to any application-specific products, except rockets and pilotless aircraft, that are insusceptible to design or program changes.) Accordingly, when exporting or carrying abroad this product, follow the Foreign Exchange and Foreign Trade Control Law and its related regulations with respect to the complementary export controls.
-
The technical information described in this document shows typical characteristics and example application circuits for the products. The release of such information is not to be construed as a warranty of or a grant of license under our or any third party's intellectual property rights or any other rights.
-
The products listed in this document are intended and designed for use as general electronic components in standard applications (office equipment, telecommunication equipment, measuring instruments, consumer electronic products, amusement equipment etc.). Those customers intending to use a product in an application requiring extreme quality and reliability, for example, in a highly specific application where the failure or misoperation of the product could result in human injury or death should first contact us.
- Aerospace Equipment
- Equipment Used in the Deep Sea
- Power Generator Control Equipment (nuclear, steam, hydraulic, etc.)
- Life Maintenance Medical Equipment
- Fire Alarms / Intruder Detectors
- Vehicle Control Equipment (airplane, railroad, ship, etc.)
- Various Safety Devices
- Traffic control system
- Combustion equipment
In case your company desires to use this product for any applications other than general electronic equipment mentioned above, make sure to contact our company in advance. Note that the important requirements mentioned in this section are not applicable to cases where operation requirements such as application conditions are confirmed by our company in writing after consultation with your company.
-
We are making our continuous effort to improve the quality and reliability of our products, but semiconductor products are likely to fail with certain probability. In order to prevent any injury to persons or damages to property resulting from such failure, customers should be careful enough to incorporate safety measures in their design, such as redundancy feature, fire containment feature and fail-safe feature. We do not assume any liability or responsibility for any loss or damage arising from misuse or inappropriate use of the products.
-
The products have been designed and tested to function within controlled environmental conditions. Do not use products under conditions that deviate from methods or applications specified in this datasheet. Failure to employ the products in the proper applications can lead to deterioration, destruction or failure of the products. We shall not be responsible for any bodily injury, fires or accident, property damage or any consequential damages resulting from misuse or misapplication of the products.
-
Quality Warranty
- 8-1.Quality Warranty Period
In the case of a product purchased through an authorized distributor or directly from us, the warranty period for this product shall be one (1) year after delivery to your company. For defective products that occurred during this period, we will take the quality warranty measures described in section 8-2. However, if there is an agreement on the warranty period in the basic transaction agreement, quality assurance agreement, delivery specifications, etc., it shall be followed. - 8-2.Quality Warranty Remedies
When it has been proved defective due to manufacturing factors as a result of defect analysis by us, we will either deliver a substitute for the defective product or refund the purchase price of the defective product.
Note that such delivery or refund is sole and exclusive remedies to your company for the defective product. - 8-3.Remedies after Quality Warranty Period
With respect to any defect of this product found after the quality warranty period, the defect will be analyzed by us. On the basis of the defect analysis results, the scope and amounts of damage shall be determined by mutual agreement of both parties. Then we will deal with upper limit in Section 8-2. This provision is not intended to limit any legal rights of your company.
- 8-1.Quality Warranty Period
-
Changes in Specifications or Suspension of Production
If your company purchases this product after one (1) year of the date of issue of the specifications or the date of your company’s last purchase of this product, whichever comes later, make sure to check for any changes in the specifications or inventory of this product. -
Anti-radiation design is not implemented in the products described in this document.
-
The X-ray exposure can influence functions and characteristics of the products. Confirm the product functions and characteristics in the evaluation stage.
-
WLCSP products should be used in light shielded environments. The light exposure can influence functions and characteristics of the products under operation or storage.
-
There can be variation in the marking when different AOI (Automated Optical Inspection) equipment is used. In the case of recognizing the marking characteristic with AOI, please contact our sales or our distributor before attempting to use AOI.
-
Warning for handling Gallium and Arsenic (GaAs) products (Applying to GaAs MMIC, Photo Reflector). These products use Gallium (Ga) and Arsenic (As) which are specified as poisonous chemicals by law. For the prevention of a hazard, do not burn, destroy, or process chemically to make them as gas or power. When the product is disposed of, please follow the related regulation and do not mix this with general industrial waste or household waste.
-
Please contact our sales representatives should you have any questions or comments concerning the products or the technical information.
Countermeasures Against ESD protection
When handling devices, devices may encounter electrostatic failure due to a static electricity discharge from the charged operator or equipment. Pay attention the following points during handling.
-
Operator
Attach a wrist strap and ground it. (Item (1) in the figure.)
[To prevent electric shock accidents and control the discharge current, ground the unit through a 1MΩ resister.]
Ensure that the human body is grounded through a 1 MΩ resistor placed in its vicinity. Otherwise, electric leakage may subject the human body to electric shocks. Do not contact the IC terminals directly, because of the electrification from the human body or clothing can amounts to several thousand volts or more.
Avoid wearing clothing containing chemical fibers that generate static electricity easily. (Item (2) in the figure.)Wear shoes for anti-static electricity. (Item (3) in the figure.) -
Equipment
Always ground the equipment that operates the IC (Mounting machine, etc.) -
Operation Table and Floor
Spread a high resistance conductive material on the table and the floor, ground it. (Item (4) and (5) in the figure.) -
Measuring equipment, tools and others
Ground the measurement equipment, tools soldering iron through a 1MΩ resistor because damage may occur if the package is charged and discharge occurs. -
Others
Recommend to install an air ionization blower. Install a humidifier if the air is dry. (Item (6) and (7) in the figure.) Do not place objects in the operation area that is easy to generate static electricity.
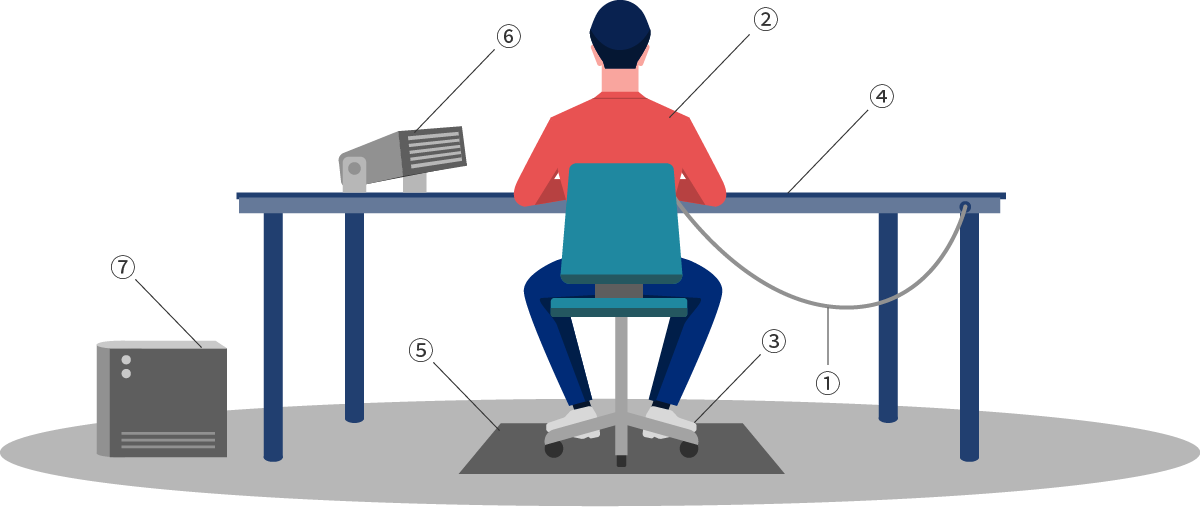
Precautions for Mounting
-
When conducting infrared ray reflow, control the temperatures of individual components with utmost care in case any differences between the resin surfaces of packages and the metal surfaces of leads in the degree of their infrared ray absorption may cause the former to have much higher temperatures than the latter.
-
Notwithstanding the recommended mounting profiles for reflow processes in mounting packages, set an actual temperature profile in consideration of various incidental factors to prohibit reliability problems.
-
When mounting through-hole type packages in the process of dip soldering in which their leads are inserted into through holes on printed circuit boards and then soaked for soldering into solder liquid in a jet soldering bath, take care to avoid direct contact of their main body with the jet solder.
-
When using a soldering iron, confirm that it is sufficiently insulated against electrostatic buildup and take utmost care to prevent any surge in its power supply from being applied to ICs.
-
When mounting packages on any equipment intended for operation at high humidity, strive to avoid electric leakage or lead corrosion by resin-coating printed circuit boards after taking appropriate measures for leaving no flux residues.
-
When mounting packages on any equipment intended to enable inspection of ICs in the midair as well as lead inspection with image recognition adopted for positioning printed circuit boards and packages, adopt a virtual planar inspection method assuming planar placement of ICs.
Note that the results of inspection of ICs by the virtual planar inspection method may differ from those of any other inspection method. -
The X-ray exposure can influence functions and characteristics of the products. Confirm the product functions and characteristics in the evaluation stage.
-
There can be variation in the marking when different AOI (Automated Optical Inspection) equipment is used. In the case of recognizing the marking characteristic with AOI, please contact our sales or distributor before attempting to use AOI.
-
Please be careful that the following environment or handling may affect internal metal corrosion of semiconductor devices.
- When using any flux, note that rosin-based flux is recommended. Please be careful not to remain corrosive constituents.
- Additionally, the product should not be used in the following environments.
- Corrosive environment (salty air, oil, rubber, automotive exhaust gases, human contamination and the like) that contains plenty of chemical constituents including, but not limited to, chlorine, sulfur and phosphorus
- Dew condensation environment
- Dusty area
- In liquid
- When using any coating or underfill to improve moisture resistance or joining strength, evaluate them adequately before using. In certain materials or coating conditions, corrosion by contained constituents, current leakage by moisture absorption, crack and delamination by physical stress can happen.
- If humidifiers are being used, provide pure water or boiled water. Keep away from corrosive gas exposure.
- Please be careful not to remain corrosive constituents.
- Use of halogen-free paste and halogen-free printed boards are recommended during board mounting.
- In case of handling products, do not touch products directly with bare hands.
-
Please be careful not to rub the product with the carrier tape when the product is picked up from the carrier tape. Because it may generate foreign matter and cause the mounting troubles.
Precautions for Measurement
Be sure to ground measuring instruments to prevent ICs from being impressed with any surge due to electric leakage. Particularly when powering on and off measuring instruments, use a clamping circuit to also prevent ICs from being impressed with any voltage or current exceeding their maximum rating from measuring instruments.
Further, take utmost care to avoid inverse or wrong orientations of ICs and short circuits between pins as well as bending, floating, and deformation of leads.
Precautions for Transportation
When transporting ICs and mounted substrates, pack them in conductive containers instead of plastic or styrofoam containers, which allow electrostatic buildup during transportation, leading to breakage’s of ICs. Similarly, when transporting ICs and mounted substrates on a belt conveyer, provide it with appropriate antistatic measures or pack ICs in conductive containers before placing them on the belt conveyer in case its rubber belt may bear electric charges.
Take utmost care to prevent vibrations or shocks from being applied to ICs and mounted substrates.
In case of carrying, if exceeded vibration, shock and drop is given, quality and reliability of component maybe cause of decline. Therefore, pay fully attention in handling.
The component shall not be used in liquid such as water, oil and chemicals.
- Lay out the product near a combustible material.
Precautions for Use
Pay attention when handling surface mount packages because the leads are thinner and can be deformed easily compared to the insertion type package. This package must be handled with care to prevent cracking due to mechanical vibration or shock, because this package is thin.
When powering on and off equipment on which are mounted packages, prevent ICs from being impressed with any voltage or current exceeding their maximum rating.
When ICs are subject to any surge, protect them by means of filters, resistors, and capacitors.
Additionally, the product should not be used in the following environments.
- Strong static electricity, electromagnetic wave and electromagnetic field environment.
- Corrosive environment (salty air, oil, rubber, automotive exhaust gases, human contamination and the like) that contains plenty of chemical constituents including, but not limited to, chlorine, sulfur and phosphorus.
- Dew condensation environment.
- Dusty area.
- In liquid.
- Lay out the product near a combustible material.
The Guideline for Removing Components
- Here are some guidelines when removing components from the board.
- Don't reuse the component after it is removed.
- The thermal profile for the process of removing components also should be optimized on each board and the component.
- It is recommended to heat the backside of the board to minimize the temperature difference at the board and the components.
- Do not remove the components when the solder is not fully liquefied, because this may cause the damage for both the components and the board.
- Extremely great care must be taken not to apply any mechanical stress to the components, especially for the components with under-filled materials. It is recommended to remove underfilled materials at the side and surface of the components.
- Here are some guidelines for removing parts during Failure Analysis.
< For MSL1 component >
- If a component is to be removed from the board, it is recommended that localized heating be used and the maximum body temperatures of any surface mount component on the board not exceed 200 °C.
- It is not recommended to use of a solder iron.
- Not following the above requirements may cause moisture/reflow damage (such as chip crack etc.) that could hinder or completely prevent the determination of the original failure mechanism.
- Rough handling can damage the component and render it impossible to analyze.
< For MSL 2 or higher >
- If a component is to be removed from the board, it is recommended that localized heating be used and the maximum body temperatures of any surface mount component on the board not exceed 200 °C.
- If any component temperature exceeds 200 °C, the board must be baked dry prior to component removal. The bake conditions is described in J-STD-033, which is published by JEDEC.
- It is not recommended to use of a solder iron.
- Not following the above requirements may cause moisture/reflow damage (such as chip crack etc.) that could hinder or completely prevent the determination of the original failure mechanism.
- Rough handling can damage the component and render it impossible to analyze.